
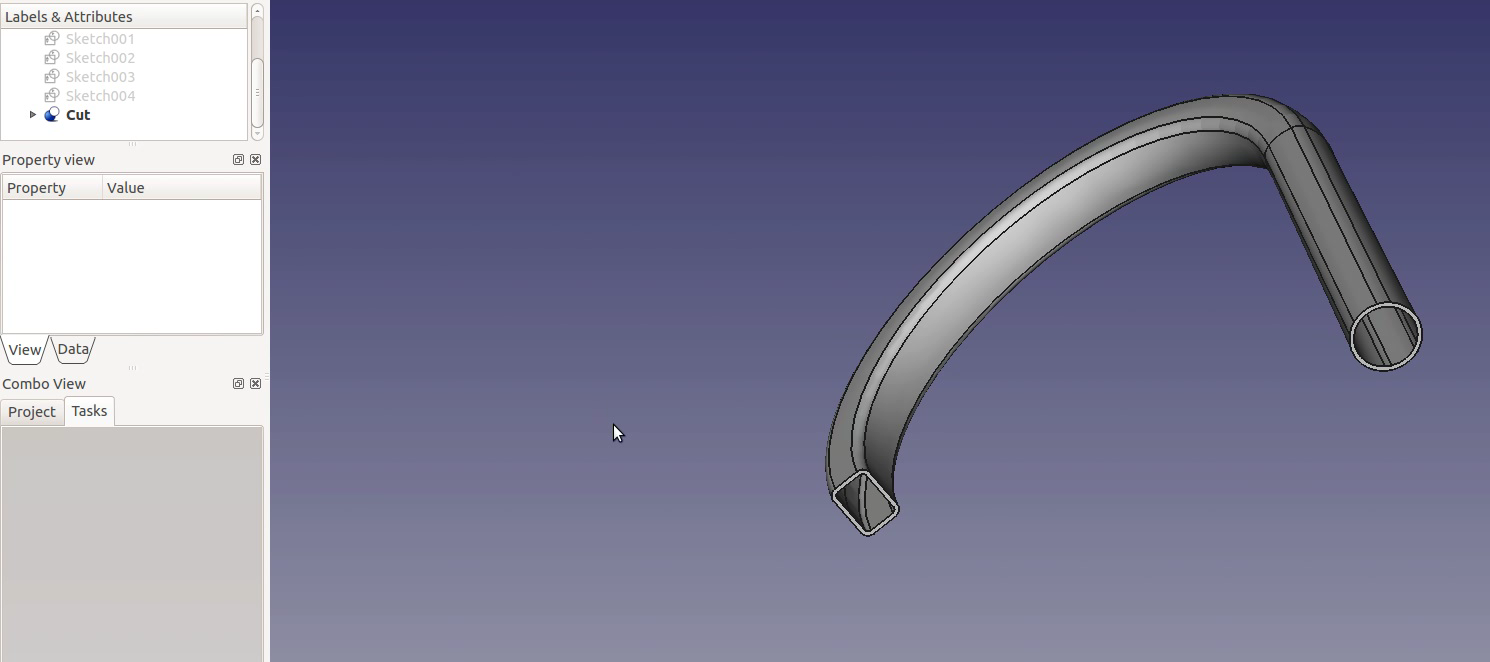
You can always move things around, but this makes it easier to think about.
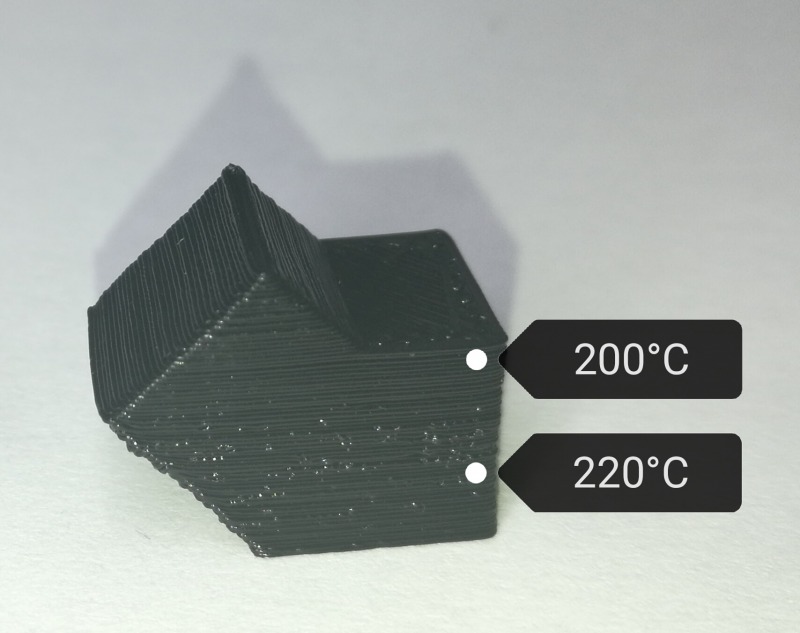
Measure the various dimensions for the 3D object.The basic process to 3D print any object is: There’s an abundance of material online, “DrVax” has a few videos on FreeCAD specific to 3D printing.īlender might also be an option and better suited to general 3D modeling, but I didn’t investigate how easy it is to use for CAD design. FreeCAD is a non-trivial program so I sought out some tutorials. The parametric modeler FreeCAD meets all these requirements so I’ve been using that, but there’s other options that might work just as well. Multi-platform (at least Mac and Windows).Precise dimensions to achieve a good fit.I decided on the following 3D modeling software requirements:
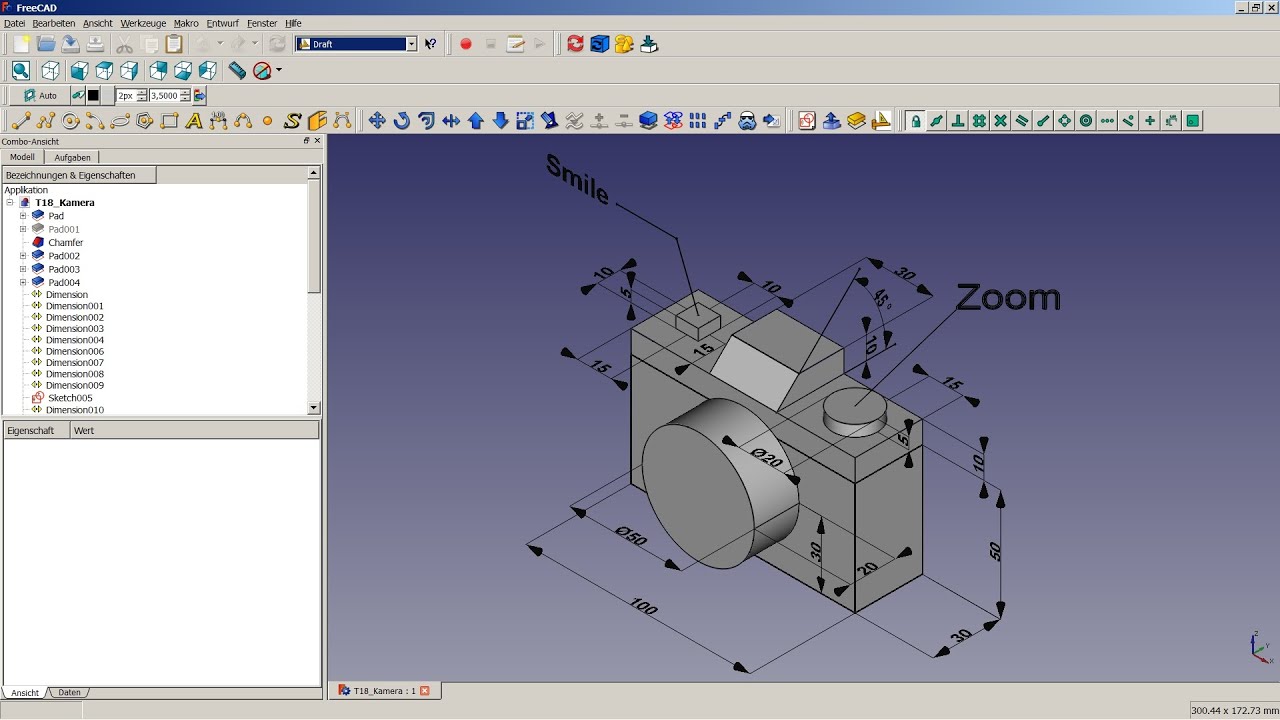
Creating 3D Modelsĭespite being in the game industry 15 years and working along-side people who use DCC tools like 3ds Max, Maya, and ZBrush everyday, I possess no 3D-modeling skills (other than briefly using MilkShape 3D in uni).
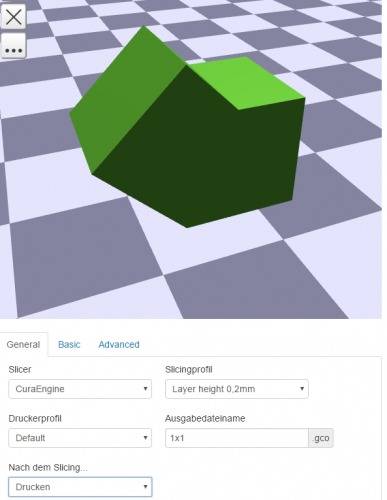
I’m just going to cover some tips to start making things with fairly precise constraints (but no moving parts). There’s already tons of resources on the web to help you pick a 3D printer, explain the different printing filament materials, tutorials on modeling and slicing, and so on. I finally got around to investigating this because I need a case for my CAPA13R mini-PC. I got a 3D printer around 2 years ago and other than the occasional dodad, it hasn’t been used for the intended purpose of printing custom cases for projects (like my solar-powered USB hardware).
